Euroglaze Aiming For Zero Errors With New Despatch System
14th February 2017
Just a single item missing from one delivery in the whole of last month might be judged a success by some medium sized trade fabricators, but for Barnsley based Euroglaze it remains one item too many. The REHAU fabricator, renowned for its commitment to continuous improvement, is aiming for zero items missing this month as it completes the first phase of its new barcoded despatch system. Customers ordering from Euroglaze can now be assured that all frames, ancillaries and cut items in every order have been checked, packed, barcoded and labelled, and that every step in that process has been recorded on camera so that any queries can be resolved almost instantly.
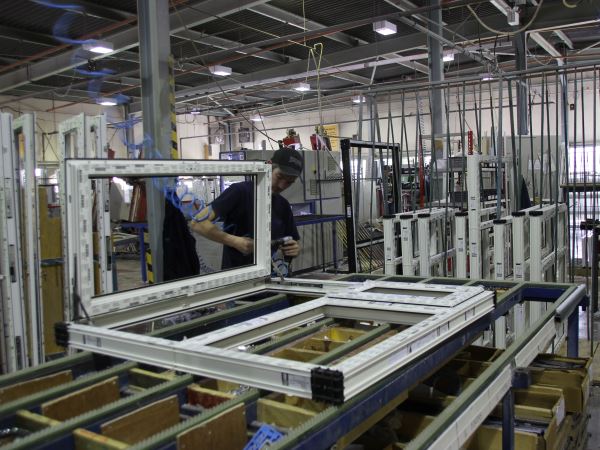
What sets the system apart is that all the items are clearly labelled with the customer’s own reference and job number and not just the Euroglaze barcode, so that they can easily keep track of what has been received. Implemented by Euroglaze’s newly appointed despatch manager Wayne Elkin, the new loading system is designed to ensure that no van can leave Euroglaze without every order being complete and in full. Pete Weston, of trade counter outlet AAC Weston in Western Super Mare, which has been a Euroglaze customer for several years, says that his business has already benefited from the new system: "We’ve got complete reassurance now that every order is complete. Obviously, this is helping us to give an even better service to our trade customers and we’ve seen a 90% drop in call backs. Because every item in the delivery is so clearly labelled and all of the bags of ancillaries are heat sealed, things just can’t get lost or muddled up. And, now that Euroglaze are videoing the whole packing process, any queries which do arise can be sorted straightaway."
Euroglaze’s Managing Director Martin Nettleton adds: "Every member of staff at Euroglaze is trained to ensure that we get deliveries right first time, but this new system gives us a failsafe and fool proof back up which goes beyond the individuals who are working here. “It’s part of a much larger programme which will see us moving more towards barcode driven production over the coming year and a more efficient paperless order processing system designed to reduce the time we spend on admin. “Fundamentally, we are always looking to become more efficient, but only in a way which benefits the distributors and installers who buy from us. We are currently, for instance, trialling the next phase of our barcode unloading system with some of our largest resellers so that we can be certain that it works just as well for them as it does for us before we roll it out across the whole of the UK."
Other Articles
Meet The Team With Alfie Booker
10th July 2025
Euroglaze Already Holds The Pas24: 2022 Secured By Design Accreditation
20th June 2025
Euroglaze Upgrades To LinkVents As Standard
4th June 2025
Do You Know Euroglaze Makes Vertical Sliders
2nd June 2025
Step Into Spring With A Grand Entrance
27th May 2025
Euroglaze Are Now Offering Fire Doors
19th May 2025
Meet The Team With Rachel Boldy
12th May 2025
Bank Holiday Approaching!
14th April 2025
Meet The Team With Katrina Evans
11th April 2025
How’s Thi Ticker?
11th April 2025